Dyecoshell™
Für uns bedeutet Langlebigkeit, dass alle verwendeten Materialien von gleicher [hoher] Qualität sind.

DIE ENTWICKLUNG UNSERES DYECOSHELL™-GEWEBES BEGANN MIT ZWEI FRAGEN:
1) WELCHEN STOFF WOLLEN WIR FÜR UNSERE TRANSIT LINE VERWENDEN?
2) WIE WERDEN WIR DEN ASPEKT DER NACHHALTIGKEIT IN ZUKUNFT ANGEHEN?
Schnell wurde uns klar, dass wir nicht einfach einen Stoff von der Stange nehmen konnten, um unsere Ziele zu erreichen. Stattdessen investierten wir mehr Zeit und Energie in die - grundsätzliche - Entwicklung eines Stoffkonzepts. Unser Ziel war es nicht "nur", eine Lösung für die Produktlinie zu finden, sondern auch einen Ansatz zu haben, der unsere Sicht auf Stoffe im Allgemeinen bestimmen würde. Bei der Definition der Anforderungen an diesen speziellen Stoff kristallisierten sich sowohl Langlebigkeit als auch Nachhaltigkeit als die wichtigsten Faktoren heraus, die es zu berücksichtigen galt.
DURABILITÄT
Für uns bedeutet Langlebigkeit, dass alle verwendeten Materialien von gleicher [hoher] Qualität sind. Das gilt insbesondere für Verschleißteile wie Reißverschlüsse und Stoffe, die über viele Jahre hinweg einer starken Beanspruchung standhalten müssen, ohne ihren ästhetischen Wert oder ihre Funktionalität zu verlieren. Bei den Stoffen war die Abriebfestigkeit für uns der wichtigste Aspekt.
NACHHALTIGKEIT
Was die Nachhaltigkeit betrifft, war der Auftrag leider nicht so klar. Wir setzten uns mit unseren Stofflieferanten in Verbindung (und fanden sogar neue), um das Thema nachhaltige Stoffe zu diskutieren, die unsere Anforderungen erfüllen würden. Wir trafen uns mit Leuten, die auf verschiedene Recyclingmethoden spezialisiert sind und recherchierten gleichzeitig nach abriebfesten Stoffen, in der Hoffnung, einen zu finden, der beide Aspekte vereint. Wir sind zwar auf interessante Ansätze gestoßen, aber die mangelnde Transparenz der meisten Recyclingverfahren hat uns noch nicht ganz überzeugt. Beim Recycling von PET-Flaschen wird beispielsweise viel Energie verschwendet und die dabei entstehenden Polyestergewebe bieten nicht die gleiche Haltbarkeit wie ein Stück reines Polyestergewebe, vor allem bei Rucksäcken.
Das Recycling von Fischernetzen, Teppichen und anderen Abfällen ist ähnlich mühsam und oft finden sich auch andere Kunststoffe wie Polyethylen und Polypropylen in der Mischung. Unterschiedliche Faserlängen und molekulare Unterschiede machen das Recycling aus verschiedenen Quellen noch schwieriger. Einige Hersteller geben auch zu, dass das recycelte Material oft nicht so belastbar ist wie sein Gegenstück aus neuem Granulat. Auch wenn die Verfahren ständig verbessert werden, sind die Ergebnisse kaum gleichwertig: Recycelte Stoffe kosten oft viel mehr und sind nicht so haltbar wie das ursprüngliche Material. Das heißt, man bekommt weniger für einen höheren Preis.
WIR GLAUBEN AN LANGFRISTIGES RECYCLING
Wir glauben, dass Recycling ein unersetzliches Element eines wirklich nachhaltigen Produktlebenszyklus ist und wir werden weiter daran arbeiten, es in unsere zukünftigen Entwicklungen zu integrieren. Im Moment glauben wir, dass es der richtige Weg für uns ist, weniger aber bessere Stoffe zu verwenden und damit Produkte zu produzieren. Deshalb haben wir nach extrem haltbaren und abriebfesten Fasern gesucht und zu diesem Zweck verschiedene Stoffe getestet, die als sehr haltbar und widerstandsfähig gelten. All diese Erkenntnisse definierten schließlich den Maßstab für unser Basismaterial. Wir wollten abriebfester sein als alles, was wir bisher verwendet haben, einschließlich der Stoffe die von Militär und Strafverfolgungsbehörden auf der ganzen Welt eingesetzt werden. Keine leichte Aufgabe.
In mehreren Versuchen haben wir Nylon 6.6 mit UHMWPE (Ultra-High-Molecular-Weight Polyethylene) kombiniert, das eine unglaubliche Zugfestigkeit aufweist und häufig für extrem reißfeste Produkte verwendet wird. Wir haben unzählige Versuche unternommen, beides zu kombinieren, sind aber über einen bestimmten Punkt nicht hinausgekommen und der hohe Einsatz des Materials stand in keinem Verhältnis zur Verbesserung der Abriebfestigkeit. Bis zu diesem Punkt haben wir festgestellt, dass die Kombination verschiedener Materialien eine schwierige Aufgabe ist (ab einer bestimmten Fadenstärke), selbst wenn wir über 100 verschiedene Abriebtests mit eigens für uns hergestellten Gewebemischungen durchgeführt haben. Am vielversprechendsten war jedoch ein speziell behandelter und gezwirnter Nylonfaden, der dicht gewebt und mit einer speziellen Beschichtung versehen ist, die wasserdicht ist dem Gewebe aber seine Bewegungsfreiheit lässt.
Das Ergebnis war ein robustes Gewebe, das (endlich) unsere Anforderungen an die Abriebfestigkeit erfüllte aber dennoch weich genug war, um Abriebspitzen außerhalb des Labors zu vermeiden, und sich angenehm anfühlte. Da sich das Nylon-Recyclingverfahren als sehr energie- und ressourcenintensiv erwies, haben wir nach anderen Möglichkeiten gesucht, um den anfänglichen Fußabdruck neuer Stoffe zu verringern. Erneut haben wir uns bei verschiedenen Herstellern umgehört, und ein Verfahren hat unsere Aufmerksamkeit erregt: DOPE DYEING.
(Einsparung von Ressourcen im Vergleich zur normalen Stückfärbung)
WAS IST SPINNFÄRBEN?
Dope Dyeing ist ein Verfahren, bei dem das Färben von Stoffen mit Chemikalien und Wasser einfach weggelassen wird. Nach dem Weben werden normale Stoffe je nach ihrer Farbe verschiedenen flüssigen Substanzen ausgesetzt. Allein der Färbeprozess verbraucht etwa 89 % des Wassers, das für die gesamte Stoffproduktion verwendet wird. Das Gleiche gilt für den Energieverbrauch (60 %), den CO²-Ausstoß (65 %) und den Chemikalienverbrauch (63 %). Damit ist das regelmäßige Färben der bei weitem ressourcenintensivste und umweltschädlichste Teil des gesamten Stoffherstellungsprozesses. Wie bei konventionell hergestellten Stoffen wird das Rohmaterial in Granulatform verarbeitet und unter Hitzeeinwirkung extrudiert. Das Ergebnis ist ein einziges dünnes Endlosfilament. Dies ist die Grundlage für jedes Garn, und eine unterschiedliche Anzahl von Filamenten, die zusammengesponnen werden, ergibt Garne mit unterschiedlicher Dicke. Normalerweise sind diese Filamente transparent bis weiß und ergeben eine Art "Off White", auch "Greige" genannt.
Beim DOPE DYEING wird das farblose Granulat vor der Extrusion mit einem farbigen Granulat gemischt, so dass das Filament direkt in der vorher definierten Farbe extrudiert wird. Beim Weben werden die bereits gefärbten Garne dann zu einem Gewebe verwoben - ganz ohne Färbung. In unserem Fall haben wir uns für zwei leicht unterschiedlich gefärbte Garne, Schwarz und Castle Rock Grey, entschieden, so dass das Produkt nicht nur das Prinzip von DOPE DYEING visualisiert, sondern auch eine Farbtiefe in den Stoff bringt, die mit regulär gefärbten Monomaterialien nicht erreicht werden kann. DOPE DYEING hat einen weiteren großen Vorteil. Ein beliebtes Beispiel ist der Vergleich zwischen einer Karotte und einem Rettich. Der Rettich hat nur eine farbige Außenzelt, während die Karotte bis in den Kern hinein orange ist. Das ist auch bei DOPE DYEING der Fall, wo der Faden durchgefärbt ist - wie bei einer Karotte. Das macht sie auch extrem widerstandsfähig gegen Ausbleichen und Verfärbung durch Abrieb und UV light. Das gleiche Verfahren wird auch bei Teppichen angewandt, die aufgrund des hohen Abriebs, dem sie ausgesetzt sind, sonst sehr schnell ausbleichen würden.
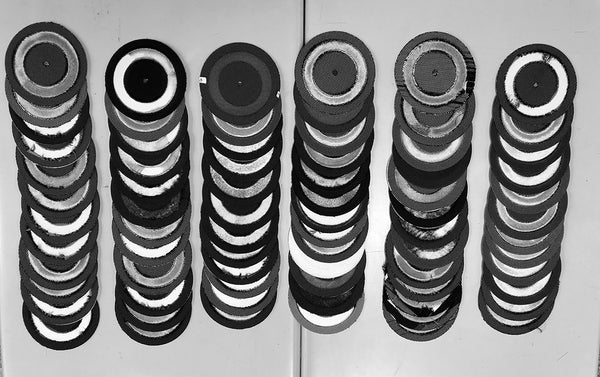
DIE LETZTEN SCHRITTE
Gemäß unserem Plan für 2018 haben wir nun die Zusammensetzung des Grundmaterials weiter verbessert und eine weitere Version zu unserer Stoffpalette hinzugefügt, die wir DYECOSHELL™ genannt haben: DYECOSHELL™. Die verbesserte Version des ursprünglichen Gewebes heißt DYECOShell I und besteht nun aus 840D Nylon x 660D Nylon, 100% dopegefärbt, 3xPU beschichtet (innen) + DWR (C6) Beschichtung (außen). Sie wird von einer leichteren Version begleitet, die wir DYECOShell II nennen und die die gleichen Zutaten enthält: 420D Nylon x 330D Nylon, 100% kettengefärbt, 3xPU beschichtet (innen) + DWR (C6) Beschichtung (außen).
Im Moment sind beide Stoffe in zwei (Garn-)Farbkombinationen erhältlich. Die ursprüngliche ist Schwarz/Castlerock, um den Unterschied in der Produktion zu verdeutlichen, und die zweite und neueste ist Schwarz/Schwarz - nun, weil wir All Black mögen. Wir werden weiterhin andere Farbkombinationen hinzufügen, trotz der Hindernisse, die der Färbeprozess mit sich bringt. DYECOSHELL™-Stoffe werden sich weiterentwickeln und das Portfolio schrittweise erweitern. Mit neuen Materialien, verschiedenen Beschichtungen und modernen Techniken werden wir unsere Produkte haltbarer und nachhaltiger machen, ohne unsere ästhetische Handschrift aufzugeben.
Zusätzlich zu den DYECOSHELL™-Stoffen ersetzen wir nach und nach unsere normalen Stoffe durch Dope Dyed-Stoffe. So besteht zum Beispiel das Futter der gesamten Transit Line aus Dope Dyed Polyester. Wir sind uns bewusst, dass wir noch nicht alle Möglichkeiten ausgeschöpft haben und dass es noch viel zu tun gibt, vor allem wenn es um Nachhaltigkeit geht, aber wir werden ständig neue Recyclingmethoden und ressourcenschonende Produktionsverfahren prüfen und nach Verbesserungen suchen.
Du möchtest mehr über unsere Technologien erfahren? Siehe auch: