Dyecoshell™ Mono
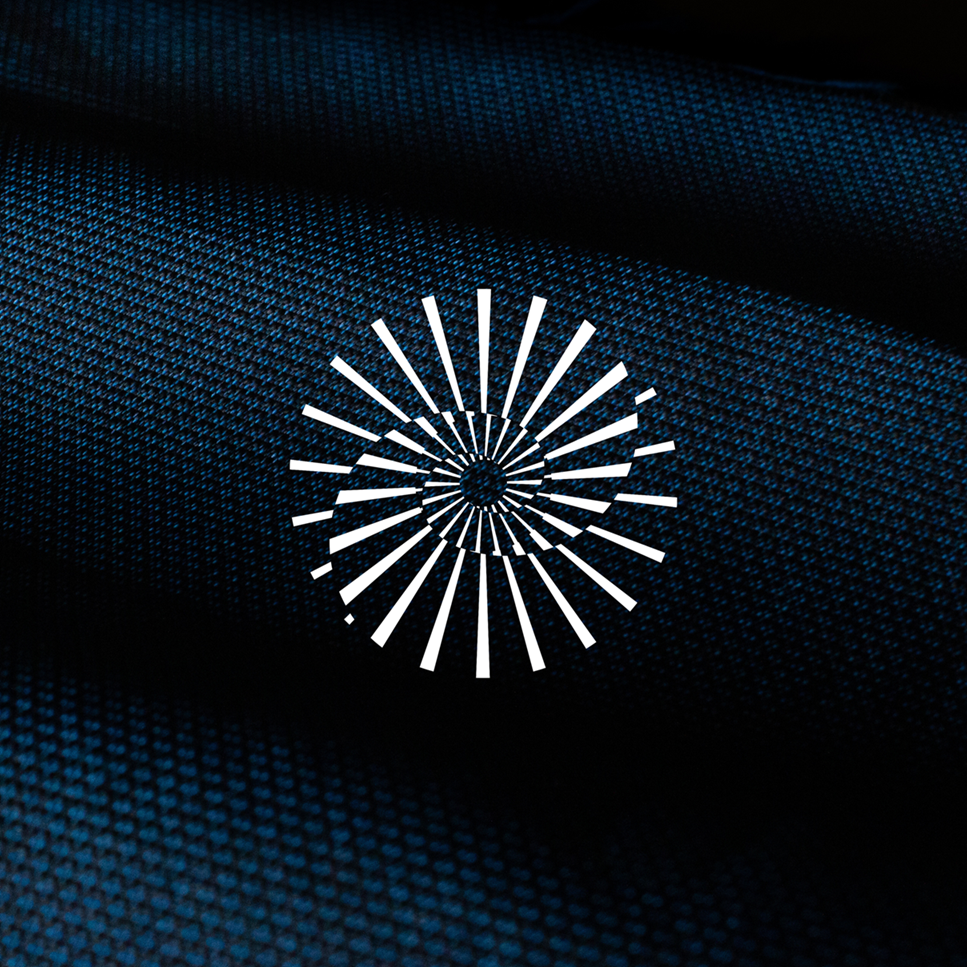
Die Bedeutung der Mono Series heute.
Im schnell wachsenden Textilsektor, in dem Modetrends immer schneller kommen und gehen, wird die Umweltbelastung durch die Produktion von Kleidung und Accessoires zu einem dringenden Anliegen. Der Beitrag der Branche zu den Treibhausgasemissionen, die Abhängigkeit von begrenzten Ressourcen und die zunehmenden Textilabfälle stellen erhebliche Herausforderungen für die Nachhaltigkeit dar.
"Ein wichtiger Schritt in Richtung der nachhaltigen Taschen-Entwicklung."
Die Einführung der Mono Series kommt zu einem entscheidenden Zeitpunkt. Mit den bevorstehenden Vorschriften der Europäischen Union, die ab 2025 die getrennte Sammlung von Textilien vorschreiben, wird die Menge an gesammelten Textilabfällen erheblich zunehmen. Dies schafft einen dringenden Bedarf an innovativen Recyclinglösungen und Produkten, die mit Blick auf ihr Lebensende entworfen wurden. In diesem Sinne verkörpert unser Mono Series Minimal Pack das Konzept des „Design for Recycling“, das darauf abzielt, Produkte mit klaren Materialströmen und recyclingfreundlichen Merkmalen zu schaffen. Mit der Mono-Series wollen wir den Taschenmarkt revolutionieren.
Auf der Suche nach alternativen Lösungen präsentiert Heimplanet Jahren der Forschung und Entwicklung die ersten Rucksack der neuen Mono Series - den Mono Series Minimal Pack. Ein vollständig recycelbarer Rucksack aus unserem eigens entwickelten Dyecoshell™ Mono Material. Der Entwicklungsprozess wurde vom Institut für Textiltechnik der RWTH Aachen und dem Fraunhofer-Institut für Chemische Technologie begleitet. Unsere Konzeptidee wurde von externen Spezialisten geprüft, um sicherzustellen, dass unser Mono-Konzept funktioniert und das Dyecoshell™ Mono Material recycelt werden kann wie geplant.

Warum ist Recycling so wichtig?
Die Kleidungsproduktion hat sich zwischen 2000 und 2015 nahezu verdoppelt, wobei der Großteil der Produktion aus Fast-Fashion-Artikeln besteht, die von minderer Qualität sind und daher zu oft ersetzt werden müssen. Darüber hinaus werden sie produziert, um aktuellen Trends zu entsprechen, was bedeutet, dass sie nicht in einen ordnungsgemäßen Nutzungskreislauf gelangen, sondern aussortiert werden, sobald ihre Attraktivität nachlässt.
Am problematischsten ist, dass ein erheblicher Teil dieser Textilien nicht recycelt wird und stattdessen auf Deponien oder in Verbrennungsanlagen landet, was die Umweltprobleme verschärft. Vor diesem Hintergrund geht die neue Mono Series einen bedeutenden Schritt zur Reduzierung des ökologischen Fußabdrucks unserer täglichen Accessoires. Durch den Fokus auf ein vollständig recycelbares und zeitloses Design adressieren wir nicht nur das Abfallproblem, sondern setzen auch einen neuen Standard für die Branche.
"Die Beziehung zu unseren Produkten endet nicht, wenn sie unsere Regale verlassen – wir übernehmen Verantwortung vor, während und nach der Nutzung der Ausrüstung."

Recycling ist nicht gleich Recycling.
Der Minimal Pack ist nicht nur vollständig recycelbar, sondern ermöglicht auch eine umweltfreundlichere Form des Recyclings. Es gibt verschiedene Arten des Recyclings, die je nach Komplexität der recycelten Güter unterschiedlich viel Energie und Chemikalien erfordern, um deren Bestandteile zu zerlegen und zu wieder nutzbar zu machen.
Mechanisches Recycling (Reißen):
Beim mechanischen Recycling werden Textilien geschreddert, um neues Garn oder Vliesstoffe herzustellen. Dabei bleibt die ursprüngliche chemische Struktur der Materialien erhalten. Obwohl dieser Prozess energieeffizient ist, resultiert er in minderwertigen Fasern (Downcycling). Um daraus wieder hochwertige Produkte herstellen zu können müssen neue Rohstoffe hinzugefügt werden. Es war klar, dass eine wirklich nachhaltige Lösung, die die Massen überzeugen soll, keine Kompromisse bei der Qualität eingehen kann. Ein rein mechanischer Prozess würde daher nie den Qualitätsanforderungen gerecht werden, die wir an unsere Produkte stellen. Mit einem fixen Ergebnis vor Augen, bleibt also die Möglichkeit den Input so weit wie möglich zu reduzieren.
Chemisches Recycling: Was ist die nächstbeste Alternative?
Im Verlauf des Forschungs- und Entwicklungsprozesses wurde deutlich, dass eine Form des chemischen Recyclings unserer Mono Series Taschen notwendig sein würde, um die hochwertigen Fasern zu gewinnen, die zur Herstellung einer „neuen“ Tasche benötigt werden. In einer kontrollierten Umgebung werden die Kunststoffe dabei in chemische Zwischenprodukte (auch Monomere genannt) zerlegt. Das Ergebnis sind hochwertige Rohfasern – im Grunde ein Material in Neuqualität, ohne dass wie beim mechanischen Recycling neue Komponenten hinzugefügt werden müssen.
Video: Vor und nach der Hydrolyse. Links sind noch weiße Partikel (gedehntes Beschichtungsmaterial) zu sehen. Gegen Ende der Hydrolyse enthält die Flüssigkeit dann kaum noch feste Partikel.
Die drei säulen der Mono Series

I. Recycelbarkeit:
Ein herausragendes Merkmal der Mono Series ist ihre Konstruktion aus einem einzigen Material: Polyester. Dafür haben wir unseren eigenen Stoff namens Dyecoshell™ Mono entwickelt. Materialmischungen in Textilien stellen eine der größten Herausforderungen für das Recycling dar, da sie aufgrund komplexer Trennprozesse oft wirtschaftlich oder technologisch nicht umsetzbar sind. Mit unserer Monomaterial-Konstruktion stellen wir sicher, dass der Rucksack einfach und effizient recycelt werden kann. Dies konnten wir erreichen, indem wir viele Komponenten durch eine Polyesteralternative ersetzt haben – 3D-Mesh statt EVA-Schaum, Webbings aus Polyester statt Polyamid, Polyester-Fleece für das Laptopfach und Polyester-Reißverschlüsse. Sogar unser Branding kommt in einer Polyesterform. Für die Hardware-Komponenten verwenden alle Heimplanet-Taschen langlebige Aluminiumteile, und dies gilt auch für die Mono Series. Um unserem Monomaterial-Konzept gerecht zu werden, haben wir dafür gesorgt, dass alle Hardware-Komponenten leicht von Hand entfernt werden können.
II. Ressourceneffizienz:
Durch die Nutzung unserer Dyecoshell™-Technologie, die bereits in den meisten Heimplanet-Taschen verwendet wird, vermeiden wir den schädlichsten und ressourcenintensivsten Prozess der Stoffproduktion – das Färben. Während Dyecoshell™ die Art und Weise, wie wir neue Produkte herstellen, verbessert hat, markiert Dyecoshell™ Mono die nächste Entwicklungsstufe unserer Stoffentwicklung mit einem klaren Fokus auf das Leben der Produkte nach ihrer Nutzung. Darüber hinaus besteht das neue Dyecoshell™ Mono Material selbst zu 50 % aus recyceltem Material in den Farben Blau und Burgund und sogar zu 100 % im Falle des schwarzen Minimal Packs. Zur Wetterfestigkeit der Taschen verwendet das neue Material eine TPEE-Laminierung anstelle der herkömmlichen und schädlicheren PU-Beschichtungen. Ressourceneffizienz gilt natürlich auch für den Recyclingprozess selbst. Wie bereits erwähnt, ist eine Form des chemischen Recyclings notwendig, um ein Downcycling zu vermeiden. Normalerweise ist chemisches Recycling energieintensiv und produziert chemischen Abfall. Dank unseres Konzepts werden jedoch sowohl der notwendige Energieaufwand als auch der Abfall erheblich reduziert. Folglich ermöglicht Dyecoshell™ Mono die Gewinnung von Quasi-Neumaterial mit minimalster Auswirkung.
III. Haltbarkeit und Langlebigkeit:
Trotz seiner Recycelbarkeit ist der Mono Series Minimal Pack sowohl ästhetisch als auch funktional langlebig. Ein langlebiges Design bedeutet weniger Ersatz und selteneres Recycling, wodurch die Umweltbelastung im Laufe der Zeit weiter reduziert wird. Abriebfeste Stoffe kombiniert mit robusten Aluminiumteilen garantieren eine verlängerte Lebensdauer. Apropos Lebensdauer: Der Mono Series Minimal Pack wird, wie alle Heimplanet-Produkte, mit einer lebenslangen Garantie geliefert, was unser Engagement für langlebige Lösungen für unsere Nutzer unterstreicht. In Bezug auf das Erscheinungsbild setzen wir auf eine minimalistische Ästhetik, um die Komplexität der Materialmischungen zu reduzieren und gleichzeitig eine zeitlose Silhouette zu bieten, die sich den aktuellen Trends entzieht.
"Der Mono Series Minimal Pack - Der umweltfreundlichste Rucksack, den wir heute herstellen können."
Wir verstehen die Mono Series als einen kontinuierlichen Entwicklungsprozess. Obgleich unklar ist, wie das endgültige Bild aussehen wird, ist klar, dass Veränderungen notwendig sind. Demnach ist es unsere Bestreben, diese Entwicklung durch innovative Konzepte weiterhin voranzutreiben und aktiv an der Förderung des Fortschritts teilzunehmen. Begleite uns auf diesem Weg und Trage die Zukunft schon Heute!
*[Deep Dive: PU vs TPEE]
- Chemische Struktur:
- Polyurethan (PU): Polyurethan besteht aus harten und weichen Segmenten, die durch Urethanbindungen verknüpft sind. Diese Bindungen sind chemisch stabil und schwer zu spalten, was das Recycling komplizierter macht.
-
TPEE: Thermoplastische Elastomere aus Ester und Ether haben eine Struktur, die leichter thermisch und chemisch abbaubar ist. Diese Materialien lassen sich durch Erhitzen und Umformen relativ einfach recyceln.
- Verarbeitbarkeit:
- PU-Beschichtung: PU ist oft stark vernetzt und bildet eine dichte, stabile Schicht auf dem Textil. Das macht das Trennen von PU und Polyester schwieriger, da starke Lösungsmittel oder hohe Temperaturen erforderlich sind.
-
TPEE-Beschichtung: TPEE ist weniger stark vernetzt und lässt sich daher leichter von Polyester trennen. Es erfordert weniger aggressive chemische Prozesse, um die Materialien zu trennen.
- Energiebilanzen:
- PU-Beschichtung: Das chemische Recycling von PU-beschichteten Textilien erfordert in der Regel höhere Temperaturen und stärkere Lösungsmittel, was zu einem höheren Energieverbrauch führt.
-
TPEE-Beschichtung: Das Recycling von TPEE-beschichteten Textilien ist in der Regel energieeffizienter, da die Trennung und Wiederaufbereitung weniger intensive Bedingungen erfordern.
- Abfallprodukte:
- PU-Beschichtung: Der Einsatz von starken Lösungsmitteln und hohen Temperaturen kann zu toxischen Abfallprodukten führen, die aufwendig entsorgt oder behandelt werden müssen.
- TPEE-Beschichtung: Die Abfallprodukte beim Recycling von TPEE sind in der Regel weniger toxisch und einfacher zu handhaben. Es fallen weniger schädliche Chemikalien an, was den Prozess umweltfreundlicher macht.